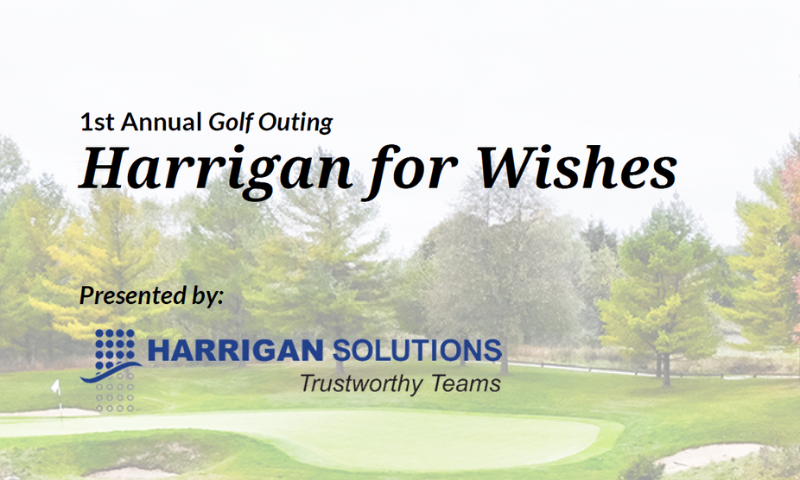
1st Annual Golf Outing Harrigan for Wishes
March 27, 2024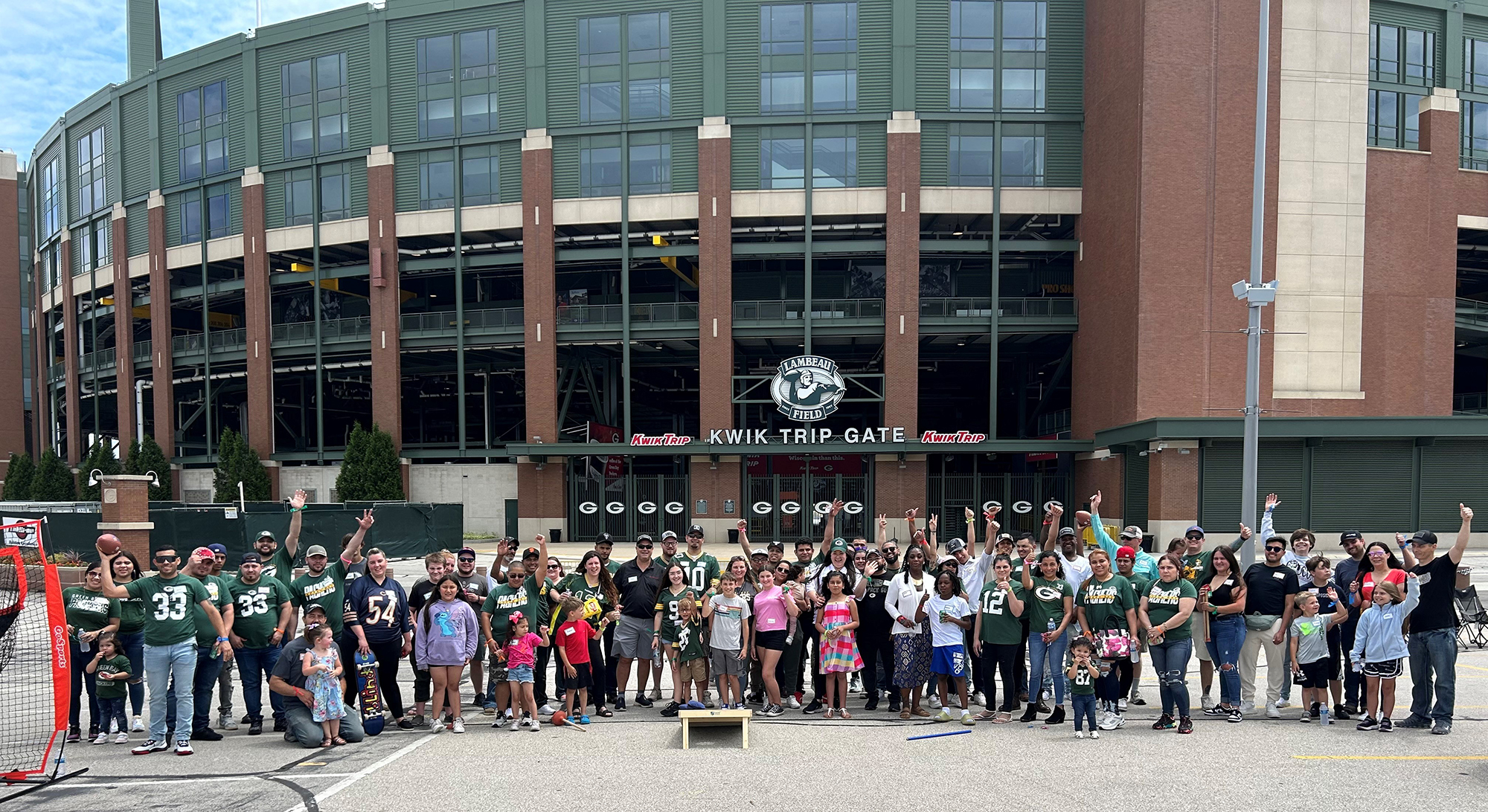
Keys to Recruiting and Retaining Great People in the Sanitation Business
September 1, 2024It’s no secret that a safe and efficient food processing facility will likely result in a profitable business model for manufacturers. Still, Harrigan Sanitation Solutions takes these goals one step further — by eliminating the food safety hazards using proven methods that provide better controls and sanitation effectiveness before manufacturing the product.
Unmotivated sanitation teams experience high turnover and put food manufacturers at risk of food contamination, production lines starting late, cost overruns, and unsafe behaviors. When comparing high- and low-engagement teams, Gallup found that high employee engagement resulted in the following differences in business outcomes: 21% decreased turnover, 63% decrease in safety incidents, 32% decrease in quality mistakes/defects, 18% increase in productivity, and 23% increase in profitability.
Harrigan operates with an above average employee turnover, sufficiently staffing our partners’ teams with award-winning employee engagement. Employees and employers thrive through a model of creating trustworthy teams invested in continuous improvement.
“Harrigan got more done with two people than we ever thought was possible,” Jon Wellik, former CEO of Ab E Manufacturing and Harrigan partner, shared. “I’m impressed with their methods and tools for employee engagement.”
When you work with Harrigan Sanitation Solutions, we collaborate to develop a realistic and goal-setting compliance plan and implementation strategy. This development process aligns with SQF, FDA, USDA, and other sanitation regulations where applicable.
Part of the Harrigan method includes monthly meetings to recap performance indicators set by the team, as well as any effort reprioritization needed or gap assessment to highlight opportunities to develop further performance.
Harrigan seeks and finds trustworthy leaders to oversee each of their sanitation teams, supervising on-site sanitation service through following SOPs and master sanitation schedules and supporting EMP programs, ensuring teams are thriving and meeting production goals. Not only are metrics met, but we go above and beyond to help team members find meaning and significance in their work and to create connections within teams to drive a positive attitude.
“In a period of five weeks, I have seen more positive change in our employees than I have seen in over four years,” Dan Moore, president of Dawn’s Foods and Harrigan partner, said. “Our employees all spoke about how the Harrigan process has not only made their work lives better, but they spent just as much time explaining how it is paying dividends in their personal lives.”
Looking to reduce risk and power profits for your customers? Reach out to Harrigan Sanitation Solutions today!